Hydraulic CNC Press Brake WATTSAN HB 6325
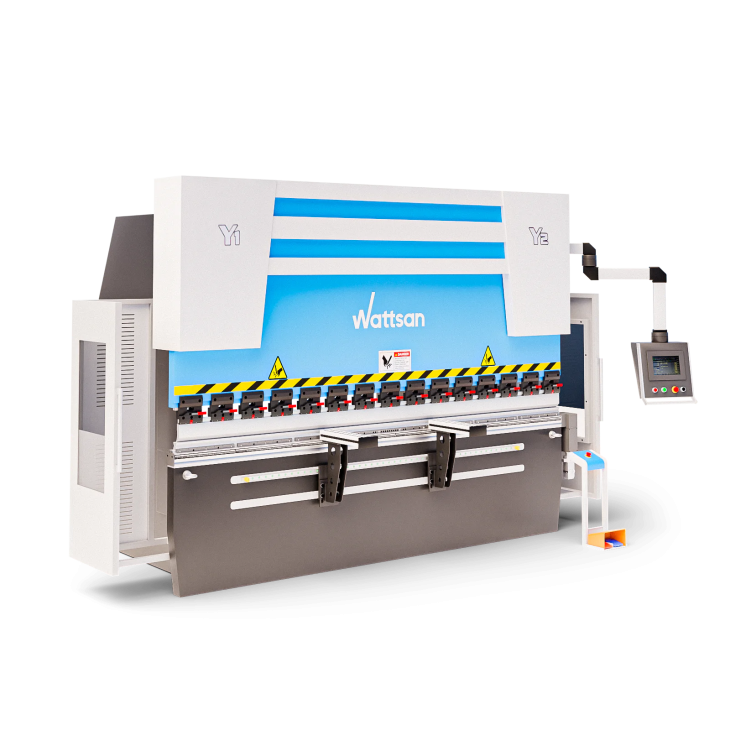
Brief of Hydralic Press Brake HB 6325
WATTSAN H-bend
Hydraulic press brake Wattsan H-bend is designed to perform bending of metal sheets of various sizes and thicknesses without preheating the metal. All-welded construction with increased margin of safety, linear guides, smart hydraulics, as well as four active independent working axes in combination with a motorized beam deflection compensation system guarantee perfect repeatability and high quality of finished products.
The use of various combinations of dies and punches allows bending at almost any angle, expanding production possibilities. This class of metalworking equipment is ideal for enterprises with a large assortment and volumes of products.
Sheet position stability at each bending stage
Purchase procedure
-
Equipment selection
We assist you in making your choice of a machine matching your needs
-
Sending invoice
We agree on the complete set of the machine and sending the invoice with the final cost of the equipment.
-
Payment
In full if the machine is in stock. 50% in advance 50% at the delivery if the machine is not in stock.
-
We check the machine
The 3 step quality control: at the Wattsan factory, at our warehouse in the Netherlands, before the delivery.
-
Delivery or pick-up
Either a transport company or you pick up the machine from our warehouse.
-
Launching equipment
We are here to assist you whenever you need support.
Experiences from enthusiastic bloggers
Technical characteristics
FAQ
-
The T-Bend series refers to NC torsion press brakes. They rely mostly on the force of levers and springs. This makes them not the most precise type, but they are strong and reliable enough for basic tasks.
The H-Bend models are hydraulic banding machines. These operate on oil and hydraulic cylinders, and the technology allows for precise control of the applied force. Furthermore, hydraulic press brakes can handle more difficult bends.
The S-Bend stands for Servo Press Brakes. Among all press brakes, this is the most accurate and quiet equipment. It is also the most environmentally friendly: it uses electricity for movement and bending while consuming less energy than a hydraulic one. The servo motors control the ram's movement, providing for the highest level of precision.
-
It’s based on your production and task complexity.
If you have a small workshop or recently established business, then choose the T-Bend series. Also, if you need to perform basic tasks at low-volume production, like creating metal tables, grills, and simple parts, this machine will serve great.
If you are looking for a machine to work at high-volume car and aerospace manufacture with strict accuracy requirements, then you need the H-Bend series. And S-Bend can provide you with even more efficiency since it’s faster and can create ideal conditions for serial production.
-
There are tools, named punch and die, that create specific angles when sheets are pressed between them. The amount of those tools makes either flexible production or strictly monodirectional machines, which can be very helpful.
-
Some of the machines may be equipped with additional tools.
First, tools for safety: laser protection system and light curtain. They both eliminate or reduce as much as possible any risk for the user.
Second, there is double-sided quick-release clamping. It makes installation of the upper tools way easier, as well as their removal. Overall, it reduces production hold-up time.
Third, an automatic laser bending angle measurement system. It helps to correct possible mistakes and make final products precise.
There are a few more. To learn more about each and figure out if you need them or not—contact our managers!
-
Actually, this equipment is quite easy to take care of. There are a few simple things to be done:
— Clean the press brake periodically to remove any dirt, dust, etc., so it won’t accumulate.
— Keep an eye on components and change them in time;
— Once a year or even less, a hydraulic press may require the oil check and change;
— Servo press brakes need regular lubrication. Other than that—not much to maintain.