Fiber metal cutting machine WATTSAN 1530 TABLECHANGE
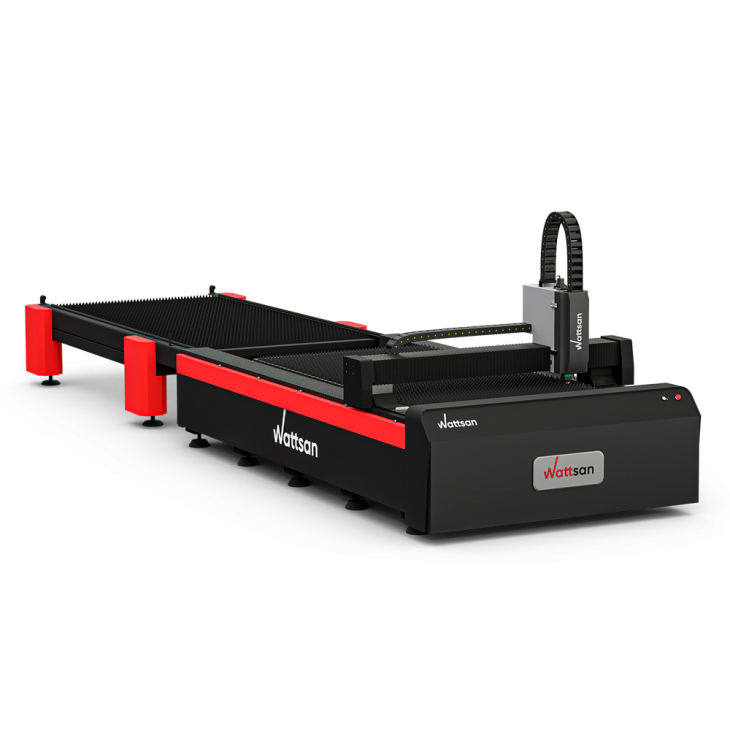
Brief of Fiber metal cutting machine WATTSAN 1530 TABLECHANGE
Wattsan 1530 Tablechange laser machine — increase the working speed by 1.5 times
The WATTSAN 1530 TABLECHANGE laser machine works with stainless and carbon steel, copper, aluminum, titanium and other materials.
WATTSAN 1530 TABLECHANGE is equipped with an automatic exchange table. Exchange tables allows you to carry out continuous operation of the machine without wasting the running time on loading and unloading products. While a metal sheet is being cut on one table, the operator collects the finished products on the second table and prepares the next sheet. This saves time on the material loading and increases the efficiency of work by 1,5 times. This machine has long been used in aircraft construction, mechanical engineering, light industry and in the manufacture of medical equipment.
The machine is equipped with a solid-state laser emitter to choose from: Max/Raycus/IPG. All three types of emitters have a service life of about 100,000 hours. This gives more than 11 years of continuous operation.
The automatic exchange table has dimensions of 1500x3000 mm for metal sheet. The table is made with a safety margin, and a large weight dampens vibrations. For additional stability, vibration mounts can be installed.
Adjust the cutting process for your production
CYPCUT software has simple user-oriented controls. The implemented functions greatly simplify and optimize the cutting process.
The machine frame is the base
Comparison table
![]() |
||||
Source power | 1000 W | 1500 W | 3000 W | 6000 W |
---|---|---|---|---|
Thickness, mm | Speed (m/min) | |||
1 | 10 | 22 | 34 | 42 |
2 | 6,2 | 6,8 | 7,5 | 8,2 |
3 | 3 | 3,6 | 4,4 | 5,5 |
4 | 2,2 | 2,8 | 3,8 | 5 |
5 | 1,8 | 2,4 | 3,2 | 3,6 |
6 | 1,6 | 2 | 2,6 | 3,4 |
8 | 1,2 | 1,4 | 2,2 | 3 |
10 | 0,8 | 1 | 1,6 | 2,4 |
12 | 0,8 | 1,4 | 2 | |
14 | 0,6 | 1 | 1,3 | |
16 | 0,8 | 1,1 | ||
18 | 0,7 | 1 | ||
20 | 0,6 | 0,9 | ||
22 | 0,5 | 0,8 | ||
24 | 0,6 | |||
24 | 0,4 | |||
![]() |
||||
Source power | 1000 W | 1500 W | 3000 W | 6000 W |
Thickness, mm | Speed (m/min) | |||
1 | 23,8 | 26,4 | 34 | 41,4 |
2 | 10,8 | 11,9 | 15,4 | 28,6 |
3 | 2,3 | 4,1 | 8,6 | 15,8 |
4 | 1,3 | 2,2 | 5,5 | 9,4 |
5 | 0,7 | 1,2 | 4,3 | 6 |
6 | 1 | 3,1 | 4,7 | |
8 | 2 | 3,3 | ||
10 | 0,8 | 1,3 | ||
12 | 0,5 | 1,3 | ||
14 | 0,8 | |||
16 | 0,6 | |||
![]() |
||||
Source power | 1000 W | 1500 W | 3000 W | 6000 W |
Thickness, mm | Speed (m/min) | |||
1 | 8,4 | 16 | 34 | 42 |
2 | 3,4 | 6,6 | 15 | 25,5 |
3 | 1,4 | 3,8 | 7,6 | 14,6 |
4 | 1,4 | 4 | 5,8 | |
5 | 3,3 | 4,9 | ||
6 | 2,1 | 4,1 | ||
8 | 0,9 | 2 | ||
10 | 0,6 | 1,7 | ||
12 | 0,8 | |||
14 | 0,6 | |||
16 | 0,5 | |||
![]() |
||||
Source power | 1000 W | 1500 W | 3000 W | 6000 W |
Thickness, mm | Speed (m/min) | |||
1 | 8 | 12 | 22 | 32 |
2 | 3,2 | 4 | 8 | 12 |
3 | 1 | 2,2 | 5,2 | 6,4 |
4 | 1,4 | 4 | 5,4 | |
5 | 1,8 | 3,2 | ||
6 | 1,4 | 2,2 | ||
8 | 0,6 | 1,2 | ||
10 | 0,6 | |||
12 | 0,4 | |||
![]() |
||||
Source power | 1000 W | 1500 W | 3000 W | 6000 W |
Thickness, mm | Speed (m/min) | |||
1 | 7 | 10 | 22 | 35 |
2 | 2 | 4 | 12 | 20 |
3 | 0,5 | 1,8 | 5 | 12 |
4 | 1 | 3 | 9 | |
5 | 2 | 6,5 | ||
6 | 1,3 | 3,8 | ||
8 | 0,6 | 1,8 | ||
10 | 1 | |||
12 | 0,7 |
High-tech equipment and verified accuracy are guaranteed
Purchase procedure
-
Equipment selection
We assist you in making your choice of a machine matching your needs
-
Sending invoice
We agree on the complete set of the machine and sending the invoice with the final cost of the equipment.
-
Payment
In full if the machine is in stock. 50% in advance 50% at the delivery if the machine is not in stock.
-
We check the machine
The 3 step quality control: at the Wattsan factory, at our warehouse in the Netherlands, before the delivery.
-
Delivery or pick-up
Either a transport company or you pick up the machine from our warehouse.
-
Launching equipment
We are here to assist you whenever you need support.
Experiences from enthusiastic bloggers
Technical characteristics
Ask questions
-
A fiber-optic laser is best suited for cutting metal, but a specially equipped CO2 laser with a high-power laser tube may also be suitable for this purpose. However, it should be borne in mind that the thickness of the metal for cutting with a CO2 laser is limited to 1.5 mm, while a fiber-optic laser is capable of cutting up to 25 mm.
-
The cost of an hour of laser cutting depends not only on the power of the laser machine and the speed of its operation, but also on a number of other factors, such as: the professional skills of the machine operator, the cost of renting a production room, the cost and consumption of electricity, the cost of the material itself, the amount of scrap and downtime of the machine, and much more. In order to unambiguously answer the question about the cost of an hour of laser cutting, it is necessary to take into account all these parameters.
-
A focused laser beam is applied to the metal surface, as a result of which it melts, the molten material is blown out of the cutting zone with the help of an auxiliary gas.
-
The power of the laser emitter depends on the thickness of the material being processed and the desired processing speed. For example, a 1 kW emitter will cut 1 mm thick stainless steel at a speed of 13 m/min, and a 3 kW emitter will cut the same material at a speed of about 35 m/min. Here everything depends on the budget and the expediency of using the maximum possible capacity. Although it can be said that in today's competitive realities it does not make sense to buy a laser machine with a power of less than 1 kW.